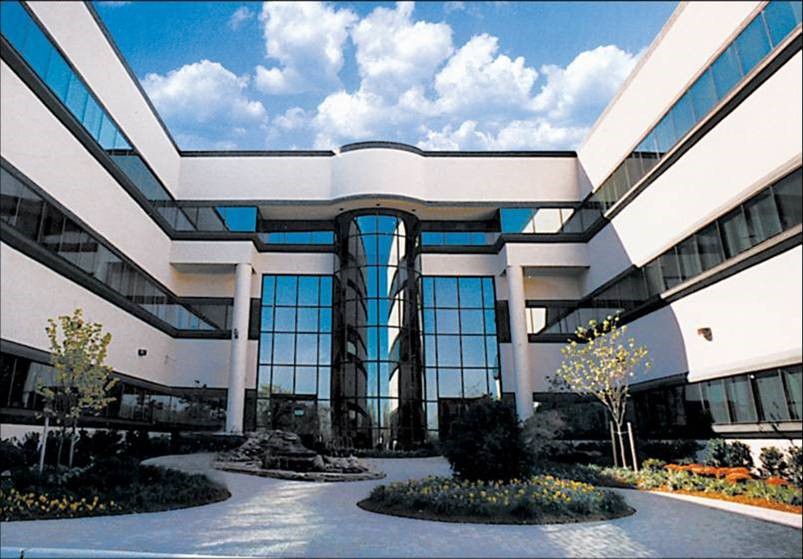
Location: Baltimore, MD, Use: Administrative
Size: 70,080 square feet, Start to Finish: Nine months
image credit: Williams Scotsman
What if you knew your building project timeline could be cut in half, your costs for construction were less, and you were able to open for business sooner with incoming revenue? To top it all off, sustainability and LEED were incorporated into the project.
Modular space solutions are more than box like structures, they can be custom built to allow unmatched flexibility and adaptability, proving that form need not be sacrificed for function. Custom interior finishes can be incorporated into the overall design of the project. Designs can be tailored to your individual needs, with unique elements and details that enable usability, as well as single story and multi-story configurability, and can be re-used over time.
This type of construction incorporates technical innovation into an automated process that uses proven, standardized practices and process efficiencies. By allowing simultaneous production of site work, as well as interior construction it reduces the overall time to occupancy. The end result: A high quality, custom solution in less time than a conventional site-built project.
Removing approximately 80% of the building construction activity from the site location significantly reduces site disruption, vehicular traffic and improves overall safety and security. So, for schools, hospitals, or other active businesses, reducing on-site activity and thereby eliminating a large part of the ongoing construction hazards, is a tremendous advantage.
By simultaneously utilizing an onsite preparation and off-site interior build out, the solution is delivered in half the time. Modular solutions provide a collaborative effort between the client, contractor and modular solution provider.
Modular solutions are not limited to trailers on a job site, they have been used to create medical facilities, hotels, educational buildings, hospitality venues, retail establishments and more.
Components of a building are custom produced inside their factory, various inspections such as electrical can be done at the factory saving time and money. Adding to the efficiencies between 60-95% of a punch list can be completed prior to the unit leaving the factory saving finish time. Building in a controlled environment reduces waste through avoidance upstream rather than diversion downstream.